Design considerations – Moving-bed reactors
Process design with MBBR is based on the concept that treatment is achieved with several reactors in series and that each individual reactor is designated for a specific treatment function within the greater treatment scheme. This is appropriate because each reactor promotes the development of a specialized biofilm oriented toward a treatment goal based on the conditions set within the reactor. This compartmentalized approach results in a rather simple and straightforward design, whereby one or more complete-mix reactors are oriented in series, each with a specified treatment purpose. Compare this with the design of a suspended-growth system, whereby competing reactions are always occurring and an overall system solids residence time (SRT) must be maintained to provide the mixture of bacterial cultures (based on growth rates and character of the raw wastewater) necessary to achieve the desired treatment goal within the hydraulic residence provided in each zone (aerated and unaerated) of the tank.
3.1. Carrier biofilms
Critical to the success of any biofilm process is to maintain a high proportion of active biomass in the reactor. When the biomass concentration on MBBR carriers is presented in terms of an equivalent suspended solids concentration, values typically are approximately 1000 to 5000 mg/L suspended solids. Yet, when performance is assessed on a volumetric basis, results show that removal rates can be much higher than those compared with suspended-growth systems. This added volumetric efficiency with MBBRs can be attributed to the following:
- High overall biomass activity resulting from effective control of biofilm thickness on the carrier resulting from the shear imparted on the carriers by the mixing energy (e.e., aeration);
- Ability to retain highly specialized biomass specific to the conditions within each reactor, independent of an overall system SRT; and
- Acceptable diffusion rates resulting from the turbulent conditions in the reactor.
Moving-bed reactors can be arranged in a number of different continuous-flow treatment schemes for BOD removal, nitrification, and denitrification.
- Site-specific conditions, including site layout and plant hydraulic profile;
- Existing treatment scheme and potential for retrofit of existing facilities/tanks; and
- Targeted effluent quality objectives.
The net effective biofilm area is a key design parameter with moving-bed reactors, and loading and reaction rates can be expressed as a function of the surface area offered by the carriers. Hence, carrier surface area is convenient and commonly used for expressing performance and loadings of MBBRs often presented as surface area removal rate (SARR) and surface area loading rate (SARL), respectively. The substrate removal rate in MBBRs is zero-order-dependent when bulk substrate concentrations are high and first-order-dependent when the bulk substrate concentration is low. Under controlled conditions, the removal rate (SARR) as a function of loading (SARL) can be expressed by the following surface reaction rate expression:
r = rmax * [L/(K+L)]
Where: r = Removal rate (g/m2*day)
rmax = Maximum removal rate (g/m2*day)
L = Loading rate (g/m2*day)
K = Half-saturation constant
General summary of treatment schemes offered by MBBRs:
Treatment objective | Process description |
Carbonaceous matter removal | Stand-alone MBBRs Roughing MBBR preceding suspended growth process |
Nitrification |
Stand-alone MBBRs MBBR following secondary treatment |
Nitrogen removal (denitrification) | Stand-alone MBBRs with pre-denitrification Stand-alone MBBRs with post-denitrification Stand-alone MBBRs with pre- and post-denitrification Post-denitrification MBBR of nitrified effluent |
3.1.1. Carbonaceous Matter Removal
The design SALR for a moving-bed reactor designated for carbonaceous matter removal will depend on the overriding treatment objective and the method selected for solids separation. The following table shows a range of typical design values for BOD loading based on application and treatment objective:
Application (objective) | SALR DBO (g/m2*day) |
High rate (75 to 80% BOD removal) | >20 |
Normal rate (80 to 90% BOD removal) | 5 to 15 |
Low rate (preceding nitrification) | 5 |
The reactor should be designed using a low loading rate when nitrification is the objective of the downstream process. Higher loading rates can be considered when only removal of carbonaceous matter removal, a bulk dissolved oxygen level of 2 to 3 mg/L is sufficient and that higher bulk dissolved oxygen levels do not help to improve the SARR.
3.1.2. High-Rate Designs
The moving-bed reactor can be considered when a compact high-rate system is needed to meet basic secondary treatment standards. In high-rate applications, the MBBR is operated under high SARL conditions, with the main purpose of removing the soluble and easily degraded BOD from the influent stream. The settling character of the biofilm slough diminishes under high loading conditions. As a result, the high-rate MBBR is combined with chemical coagulation and flocculation of the treated effluent, flotation, or with a solids contact process step to remove the solids; however, overall, this results in a compact system capable of meeting basic secondary treatment standards in a short hydraulic retention time (HRT).
3.1.3. Normal-Rate Designs
The moving-bed reactor offers a technology option when conventional basic secondary treatment approaches are being considered. Typically, two reactors in series are considered to achieve this level of treatment. To summarize 7-day BOD (BOD7) removal performance at four normal-rate MBBR WWTPs designed for BOD removal followed by chemical removal of phosphorus: In these cases, the MBBRs were designed with an organic loading rate of 7 to 10 g BOD7/m2·d at 10 ºC and are combined with follow-up chemical addition and flocculation for phosphorus removal and enhanced solids separation.
3.1.4. Low-Rate Designs
A low loading-rate design should be considered for reactors designated for organic matter removal upstream of a nitrification reactor. This helps to ensure that a high nitrification rate can be achieved in the downstream nitrifying moving-bed reactor, which, in turn, results in the most economical design. In instances where the BOD load to the nitrification MBBR is not sufficiently reduced, the nitrification rate will be reduced significantly, and the reactor may be ineffective.
This would be the case in a situation where a BOD load that was too high was selected for the prior organic matter removal stage of treatment, resulting in carryover to the nitrification stage of treatment, resulting in carryover to the nitrification stage of treatment. As an example, the figure shows that a nitrification rate of 0.8 g/m2·d could be achieved at a BOD load of 2 g/m2·d and a bulk dissolved oxygen of 6 mg/L, but would be reduced by roughly 50% if the BOD load increased to 3 g/m2·d. the operator could adjust by using a higher bulk dissolved oxygen level to help compensate for the impeded condition, or the fill fraction could be increased to reduce the surface area loading rate. However, it is important to note that neither of these options results in an economical and effective design approach. Rather, the preferred design approach would be to size the MBBRs designated for BOD removal by using a conservative low loading rate, so that the maximum efficiency can be attained in the downstream nitrifying MBBR.
During a study, two separate bench-scale nitrification rate tests were conducted 6 weeks apart on carriers taken from each of the three MBBRs. For each test, nearly identical conditions (i.e., dissolved oxygen, temperature, pH, and initial ammonia concentration) were maintained in each of the three bench-scale vessels. The rate test results show that the first reactor, which was loaded at the highest soluble COD (SCOD) loading rate (5.6 g/m2·d), provided little, in terms of nitrification, but was successful in its function of reducing the SCOD load before the second reactor. This is exhibited by the following:
- High nitrification rates observed for the second reactor, which were close to the rates observed in the third reactor,
- Small difference between the soluble COD loading condition in the second reactor compared with the soluble COD in the third reactor.
For low rate designs where it is important to select a conservative SALR, a temperature correction factor can be used to adjust the SARL based on wastewater temperature.
3.1.5. Nitrification
A number of conditions within a nitrification-stage MBBR must be considered for proper design, as these have a significant effect on reactor performance. The most significant factors are:
- Organic loading,
- Dissolved oxygen concentration,
- Ammonia concentration,
- Wastewater temperature, and
- pH/Alkalinity
We illustrated the importance of removing the organic matter present in the wastewater before reasonable removal rates will be achieved in the downstream nitrification MBBR. Otherwise, heterotrophic biofilm competition for space and oxygen reduces (or eliminates) the nitrifying activity of the biofilm. As the organic loading is reduced, the nitrification rate increases, until the dissolved oxygen concentration becomes rate-limiting. Substrate availability (ammonia) only becomes rate-limiting when concentrations in the reactor are low (<2 mg N/L) and therefore is a concern when substantially complete nitrification is required. In these cases, two reactors in series may be considered, whereby the first reactor is oxygen-limited and the second reactor is ammonia-limited. As with all biological processes, temperature has a marked effect on the nitrification rate, but this can be offset with MBBRs by operating with a higher bulk dissolved oxygen concentration. Finally, at low alkalinity levels, the nitrification rate within the biofilm will begin to show inhibition. The following subsections discuss each of these important design factors.
In applications where sufficient alkalinity and ammonia is present (at least initially), the nitrification rate will increase as organic loading is reduced, until the dissolved oxygen concentration becomes rate-limiting. In well-established nitrifying MBBR biofilms, the availability of oxygen limits the rate of nitrification on the carriers, as long as the O2-to-NH4-N ratio is below 2.0. thus, unlike suspended-growth systems, the reaction rate in a moving-bed reactor exhibits a linear or near-linear dependence on the bulk dissolved oxygen concentration under oxygen-limited conditions. This observed behavior is likely from the rate at which oxygen diffuses through the stagnant liquid layer and penetrates the biofilm. A higher bulk oxygen concentration increases the concentration gradient through the biofilm. The increased mixing energy under higher aeration velocities also helps to improve transfer from the bulk liquid to the biofilm. If organic loading is held constant (i.e., biofilm thickness and composition), the nitrification rate can be expected to increase linearly with an increased dissolved oxygen concentration. Until fairly low bulk liquid ammonia concentrations are observed in the reactor, an increase in bulk dissolved oxygen level helps increase the nitrification rate.
Though dependency of nitrification kinetics on temperature can reduce nitrification rates at the governing “wintertime” design temperature, this effect can be offset with MBBRs by the combined effect of higher attached biofilm concentrations on the carriers typically observed at colder temperatures and by maintaining higher bulk dissolved oxygen levels in the reactor. At colder wastewater temperatures, a higher biomass (g/m2) commonly is observed. Also, higher bulk dissolved oxygen levels can be attained without an increase in aeration velocity, as a result of its higher solubility at lower liquid temperatures. In net, the nitrification activity per unit surface area of carrier can be maintained effectively despite a reduction in the specific biofilm activity (g NH3-N / m2·d ÷ g SS /m2).
Figure 5.8a shows the seasonal observation of increasing and decreasing biomass as a function of wastewater temperature at a tertiary nitrifying MBBR installation. As shown, the biomass concentration drops significantly between May and June as the wastewater temperature warms from <15 ºC to >15 ºC. Two data clusters are grouped by wastewater temperature conditions (>15 ºC and >15 ºC) and are shown on Figure 5.8b.
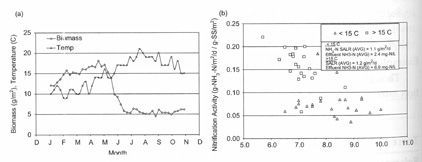
Figure 5.8b
Though the specific biofilm activity is lower for the <15 ºC data set, overall performance is maintained by a higher overall biomass concentration and by a higher bulk dissolved oxygen level as a result of an increase in gas solubility at lower temperatures. The observation helps depict that an overall surface area reaction rate on the carriers can be maintained during colder temperature conditions offset by an adapted biofilm, despite a reduction in the nitrifier growth rate.
3.1.6. Denitrification
Moving-bed reactors have been used successfully for denitrification in pre-, post-, and combined configurations. As with other biological denitrification processes, the main factors that must be considered in design are the following:
- Presence of a suitable carbon source in a proper carbon-to-nitrogen ratio in the reactor,
- Level of denitrification required,
- Wastewater temperature, and
- Oxygen carryover from upstream process steps or recirculation flows.
3.1.6.1. Pre-Denitrification Moving-Bed Biofilm Reactors
Pre-denitrification with MBBRs is typically well-suited in instances where BOD removal, nitrification, and a moderate level of nitrogen removal are needed. The influent to the reactor should have a favorable ratio of easily biodegradable COD and ammonia (C:N) to make efficient use of the anoxic reactor volume. The dissolved oxygen returned in the recycle flow can have a significant influence on performance with MBBR systems, because elevated bulk dissolved oxygen levels can be required for the nitrification stage of the MBBR process. This can place a practical upper limit on the most effective recirculation ratio (Qrcy:Qinf), whereby a further increase in the recirculation rate ends up reducing the overall denitrification efficiency. Where influent wastewater characteristics are suitable for pre-denitrification, nitrogen removal performance typically can range between 50 and 70%, with a Qrcy:Qinf ratio of 1:1 to 3:1.
3.1.6.2. Post-Denitrification Moving-Bed Biofilm Reactors
Post-denitrification with MBBRs may be considered in instances where the degradable carbon naturally present in the wastewater is insufficient or has already been depleted by an existing upstream process, or when limited space availability at the plant-site calls for compact high-rate denitrification. Because performance is not limited by factors such as internal recycle rate or carbon availability, high levels of nitrogen removal (80%) can be achieved within a minimum HRT.
If there are stringent limits on effluent BOD and low nitrate levels are required, it may be necessary to follow post-denitrification with a small post-denitrification MBBR. Practical experience has shown that post-denitrification performance in MBBRs can be inhibited when precipitation treatment upstream of the reactor results in phosphorus-limiting conditions for cell synthesis.
Maximum nitrate SARRs with external carbon addition can be greater than 2 g/m2·d when carbon is added in excess.
3.1.6.3. Combined Pre-/Post-Denitrification Moving-Bed Biofilm Reactors
Moving-bed reactors can be combined to take advantage of the economy provided with pre-denitrification and the performance of post-denitrification. The pre-denitrification reactor can be designed so that it can be operated as an aerated reactor during the winter months when
- Additional aerated reactor volume would be helpful for improving nitrification performance, and
- The cold wastewater temperature results in high dissolved oxygen levels and lower soluble CODs, which otherwise would impede pre-denetrification efficiency.
During the winter months, the post-denitrification reactor would be relied on to provide all required nitrate removal.
3.2. Mixers
In denitrification MBBR applications, rail-mounted submersible mechanical mixers have been used to circulate and mix the contents of the reactor and mix the carrier media. Some special considerations are required for a proper design. These are (1) location and orientation of mixers, (2) type of mixer, and (3) mixing energy.
With a specific gravity of approximately 0.96, the biofil carriers will float when there is no energy added to the reactor. This is different from suspended-growth systems where, in the absence of energy, the solids will settle. As a result, the mixers needed to be located toward the surface of the reactor, but no so close as to create a vortex on the surface, which could entrain air into the reactor. The mixer unit needs to have a slight negative inclination, to help push the media down into the lower depths of the reactor, as shown in Figure 5.10. In typical applications, unaerated MBBRs require between 25 and 35 kW/m3 to mobilize the floating bed of media.
Special mixing considerations are required for denitrification MBBRs. Not all mixers are suitable for long-term use in an MBBR.
The mixing energy required to properly mix a denitrification MBBR depends on the fill fraction of media and the biofilm growth anticipated in the reactor. Practical experience has shown that reactor mixing is more effective at lower fill fractions (e.g., <55%). A high fill fraction can make it difficult for a mixer to successfully circulate the media and should be avoided. Instead, a lower fill fraction with higher surface area loadings – and hence a higher biomass concentration – on the carriers helps to weigh down the media, making it easier for the mixers to circulate the media within the reactor. For this reason, it is important to select a size of denitrification reactor such that the fill fraction is amenable to mechanical mixing.
3.3. Pretreatment
As with many of the other submerged biofilm technologies, MBBRs need to have proper preliminary treatment upstream of the reactor. Good screening and grit removal is required to prevent long-term accumulation of undesirable inert materials in the MBBR, such as rags, plastics, and sand. These materials are difficult to remove once they have entered the reactor, because the reactor is partly filled with carrier media. Manufacturers generally recommend no larger than 6-mm spacing if primary treatment also is provided. Still, finer screening at 3 mm or less is mandatory in instances where primary treatment is not provided. On the other hand, add-on MBBR processes, where significant treatment already occurs upstream, likely do not need additional screening.